钛冶金通常采用氯化冶金的方式从钛铁矿或富钛料中将钛元素以四氯化钛形式提取出来,再根据下游产品选择还原或是氧化来生产金属钛或者氧化钛。而钛的氯化冶金根据其反应的不同主要分为熔盐氯化和沸腾氯化两种。
沸腾氯化由于其具有产能大、不产生废盐等优势,是近年来四氯化钛生产的主流工艺,尤其是国际上的氯化法钛白粉生产技术均是采用沸腾氯化法生产工艺。钛冶金过程的沸腾氯化主要在沸腾氯化炉内进行,而内衬材料则是沸腾氯化炉重要的组成部分,是关系到其能否正常使用和运行的关键。
一、氯化炉内衬结构简介
整个沸腾氯化炉内衬的主要作用是形成气流边界,形成撞击流的约束,使得物料合理流态化。并在高温反应下起到隔热、绝热的作用。在整个运行过程中,氯化炉内成分十分复杂,主要成分为:高钛渣颗粒,TiCl4、Cl?、O?、CO、CO?、N?等。沸腾氯化炉主要分为以下几个部分:
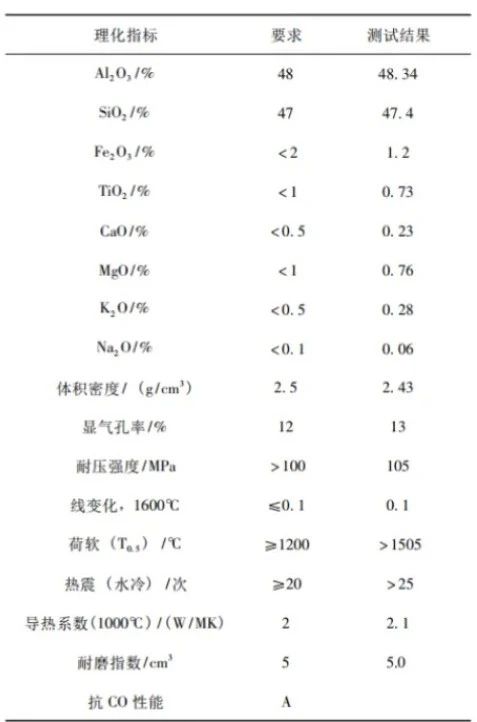
图1 氯化炉示意图
(一)炉底和反应段
由于沸腾氯化炉的特殊结构,氯气进气口主要安装在该段,均匀地分布在四周。在通入气体后,形成撞击流,在炉底和四周内衬的约束下,形成向上的流态化反应床层。炉底和反应段内衬正常工作温度为900~1000℃,这一区域主要承受炉料在撞击流作用下的直接冲击和摩擦作用。该部位因承受物料的冲击、上升的磨损气体侵入、碳沉积发生反应而容易发生内衬材料的损坏。其损坏原因主要有:
1、热的作用:即热负荷、热冲击;
2、化学作用:由于氯气、碱金属、渣等化学元素的侵入,造成内衬材料渣化和损坏,以及氯气与耐火材料的化学作用;
3、机械作用:由于物料颗粒的摩擦和含尘烟气磨损造成内衬材料的受损。
(二)进料段
在该部分周期地进料(依据工艺而定),特别在进料口中采用了特殊的材料,以减少固体颗粒物的磨损。但由于工艺的操作,反应段的升降,大量的流态化高温流对该部分的内衬的冲刷是主要的破坏因素,特别是进料口附近的内衬是冲刷厉害的部位。
1、过渡段。过渡段在反应段与炉底之间起过渡作用,该部位的温度在800℃左右,过渡段炉衬主要与未反应的物料接触,受到物料的侵蚀作用并不大。
2、扩大段。沸腾氯化炉上部是用于降低气流速度,而使得未反应的物料在重力作用下返回至反应段继续进行反应,有效利用物料。
二、氯化炉内衬损坏机理分析
(一)炉衬材料的成份及矿物组成
沸腾氯化炉内衬材料主要采用Al?O?和SiO?,物相组成主要为莫来石,主要化学成份及物理性能测试见表1。
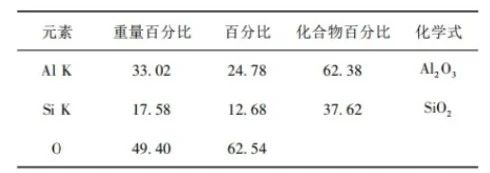
表1 氯化炉炉衬材料要求及测试分析结果
(二)氯化炉炉衬材料损坏过程研究
从热力学上看,Al?O?-SiO?系材料[4]各物相在氯化反应中:莫来石相(A?S?)非常不稳定,其成份见表2,石英相(SiO?)非常稳定,刚玉相(Al?O?)居中;在碳热还原中:石英相非常不稳定,刚玉相非常稳定,莫来石相居中。在实际中,炉衬材料是如何损坏的,其过程是怎样发生的,这要从残砖显微结构分析入手。
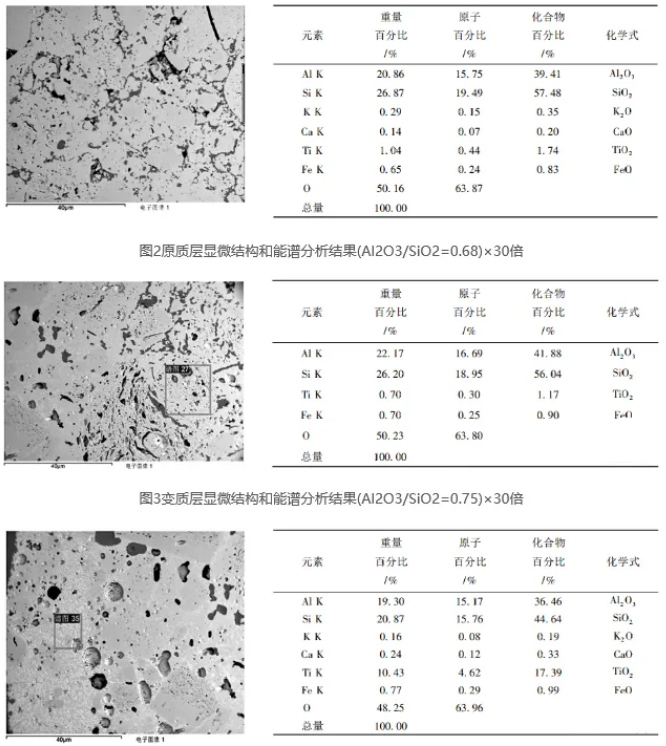
表2 莫来石成分
取氯化炉内残砖,按原砖层、变质层、反应层切片,采用6300SEM电子显微镜,能谱采用OXFORD硅锂检测器,对砖不同层进行分析研究,如图2、图3、图4所示。
图片
从残砖显微结构和能谱分析结果来看,从原质层、变质层到反应层,炉衬材料中(主要为莫来石相和石英相)的Al2O3/SiO2比值是不断升高的,说明炉衬材料中的SiO2是向外不断“流失”的。从动力学上来,耐火材料中的SiO2以固相形式向外迁移是十分困难的。从热力学上看,在砖内部(变质层)没有C参与反应的情况下,Cl2与SiO2反应形成SiCl4,以SiCl4气体形式向外迁移是不可能的。因此,在氯化炉工况条件下,炉衬材料中内部SiO2的“流失”现象只能以SiO气体形式向外迁移,这可能是SiO2碳热还原反应所引起。SiO2碳热还原反应过程如下:
(1) SiO?+2C=Si+2CO(g)
(2) Si+C=SiC
(3) SiO?+3C=SiC+2CO(g)
(4) SiO?+C=SiO(g)+CO(g)
(5) SiO(g)+2C=SiC+CO(g)
(6) SiO(g)+C+2Cl?(g)=SiCl4(g)+CO(g)
(7) SiO?+CO(g)=SiO(g)+CO?(g)△G=△G0+RTln(PSiOPCO?/PCO)
根据相律,在Si-C-O系统在不变点同时可有5个以上的相:P=3+2=5。即在形成SiC的温度条件下,此反应开始发生温度为1350℃左右,该Si-C-O系统可含有下列单独物质:C,Si,SiO,SiO?,SiC、CO和CO?。
在C过量并直接参与反应的情况下,反应中不存在CO?。从动力学角度看,基元反应多数是单分子反应和双分子反应,三分子反应不多,四分子反应更少,所以除少部分紧密结合、相互包围的SiO?与C直接通过式(3)所示固相反应生成SiC晶核之外,SiO?与3个C分子同时相遇发生反应的几率较小,即式(3)所示反应发生的程度非常有限,更应被视为几个加合反应的总反应式。
在Si-C-O系统反应中,C和SiO?为反应原料,Si和SiO是反应的中间产物,SiC和CO为末尾产物。Si的熔点为1410℃,沸点为2355℃,而SiO在1180℃以下任何温度都不稳定,在高温下以气态存在,所以中只存在SiO?、C、CO、SiO、SiC等几种可能的物相。
可以确定,碳热还原SiO?的基元反应步骤为:
SiO?+C=SiO(g)+CO(g);SiO(g)+2C=SiC+CO(g)
但事实上有Cl?存在,SiO?碳热还原的基元反应中,第2步可能没有按式(6)进行,而是按式(7)进行,从而导致炉衬材料中SiO?的不断“流失”。在残砖的表面反应层,SiO?的“流失”可能是按此过程损毁的,这与残砖反应层显微结构中看不到SiC是相吻合的。
在C过量但并不直接参与反应的情况下(即PCO/PCO?比值较大),反应中不存在C,那么SiO?碳热还原的反应将按照式(7)进行。经过热力学计算,式(7)反应开始温度为1400℃左右。炉衬残砖在炉况不正常超温情况下形成变质层,其中的SiO?的“流失”可能是按此过程损毁的。
三、结论
从前面的分析可知,氯化炉炉衬材料的损毁速度主要受Al?O?-SiO?材料中碳热还原速度的控制。其损毁过程为:
在砖内部,外部的CO气体通过材料的孔隙向材料内部扩散,与SiO?发生碳热还原反应生成SiO和CO?气体向外部扩散,到达砖表面时,SiO气体与表面的C和Cl?反应生成SiCl4气体,SiCl4气体向炉内扩散。而CO气体与SiO?的碳热还原反应导致材料结构松散,进一步形成外部CO向砖内部渗透的通道,如此反复,直到砖内部CO压力小到无法与SiO?发生碳热还原反应或达不到反应温度为止。
在砖的表面,SiO?直接与C发生碳热还原反应生成SiO和CO,生成的SiO又与C和Cl?反应生成SiCl4,直接向炉内扩散。
外部夹杂着TiO?微细颗粒的TiCl4气体通过SiO?碳热还原反应形成的通道,则不断向砖内部渗透,形成Al?O?-SiO?-TiO?液相(TiCl4对此相图的影响无资料报道),从而加速材料的结构解体,导致耐磨性能急剧下降。
无论在砖内部或表面,莫来石颗粒基本均保持了其原颗粒形貌,再次证明了其损毁速度是由碳热还原速度控制的,与氯化反应速度无关(虽然从热力学上莫来石容易发生氯化反应)。
四、氯化炉炉衬的优化建议
(一)材料的选用
1、炉衬材料选用氧化铝含量较高的Al?O?-SiO?系砖是十分必要的。
2、炉衬材料选用高纯的电熔莫来石和电熔刚玉为主要原料将可以有效提高其寿命,并可以在更大范围内容忍操作工艺上的波动。
3、在保证砖热震性能的基础上,降低砖的气孔率和提高热态强度(耐磨性能)十分关键。
4、选择合理的制砖级配和结合剂是保证刚玉-莫来石砖在氯化炉上长时间使用的技术核心。
(二)结构优化设计
依据不同部位的损情况进行改造。改造后的炉体结构为:用耐磨性更强的电熔莫来石、电熔刚玉砌筑于进料口位置。而在其他的部位一层采用氧化铝含量稍低的高铝砖,二层则和第三层采用氧化铝含量更低的高铝砖或粘土砖。
这样的结构即可以增强炉体的强度,又提高了炉体的气密性,防止氯气从砌缝中泄漏,同时也降低使用成本。其维护保养也简单,每次维护只需要对损坏部分进行替换即可,每次维护后大约可连续使用一年左右,并且每次的维护时间大约一周,有效的提高的生产效率。
上述结构的改造,是结合炉衬损坏机理及氯化冶金工况进行理论上的优化设计,还需要在实践过程中不断地改进,在使用寿命和成本上综合考虑。